Not only are costs rising due to inflation and supply chain disruptions, but there also is an ongoing skills crisis.
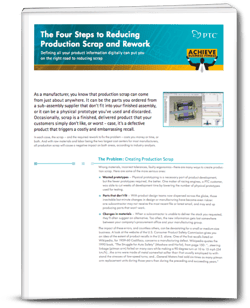
Tool-wear and failure may not be detected with a manual preventive maintenance strategy, and data may be omitted through error, bias, or training issues. DMI has been in business since 1970, has a successful track record, history and is financially sound. By investigating and analyzing the defects of each rejected product, we could identify a number of actions to improve our production processes as well as product quality. Scrap rate can be used as a KPI (Key Performance Indicator) to measure the quality of the production output in a specific manufacturing process. Reducing scrap in manufacturing processes means more than just making cuts efficientlyit requires using the right tool for the job to maximize efficiency. Ill-fitting, damaged, or poorly-made tools can be a source of scrap, not to mention safety risks. Traditional maintenance doesn't predict subtle, deeply embedded data such as vibration, oil and lubrication consistency, particulate content, and other factors. This means that all procedures in the production process must be completed in the As the proliferation of the Industrial Internet of Things (IIoT) progresses, there will come a time when few companies without connectivity will survive. Most scrap will be related to the waste identified in the six big losses: Root cause analysis can be conducted for each type of scrap loss and process changes can be implemented to reduce or eliminate the scrap. All raw materials such as metals and plastics are sorted for recycling as well as other waste such as cardboard, paper, and wood.
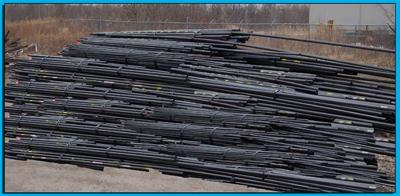
But highly volatile disruptions, unpredictable business climates, and increased demand and competition have forced companies to address business agility as an imperative. Even tooling alone can be expensive! Copyright 2022 by Elos Medtech AB. Operators, technicians, and managers relied upon a sea of charts, graphs, forms, and, The goal of every manufacturer is to produce goods in the fastest manner possible with the lowest volume of quality rejections. Many manufacturers are drowning in written documents from manual procedures.
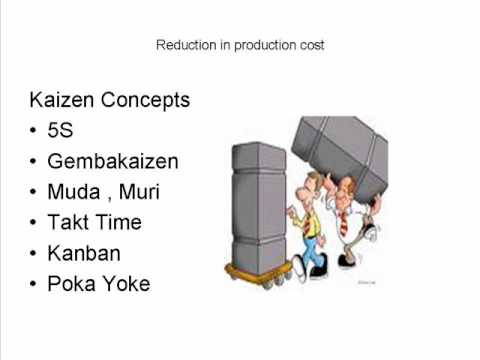
It often has a monetary value and is usually recyclable. Monitor production analytics and conduct root-cause analysis faster to identify process optimizations that reduce waste. This site is protected by reCAPTCHA and the Google Privacy Policy and Terms of Service apply. So, these money saving baskets end up costing more in the way of manufacturing scrap and wasted time than they save in up-front expenses. This is because processes veer over time, and control mechanisms to account for and adjust these changes have always been manual. Without understanding the current process as it occurs, identifying scrap points would prove impossible. Standard operating procedures (SOPs), CAD drawings, and bills of materials (BOMs) should all be documented digitally and filed correctly to ensure scrap and rework arent caused by someone referring to an outdated document. Website Last Modified July 29, 2022.
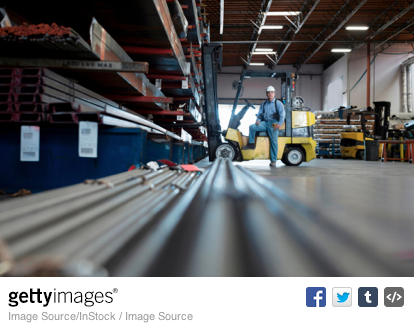
Marlin Steel is a leading manufacturer of customengineered products from steel wire And whether standalone or as part of a broader ERP system, MES has played a significant part in managing and improving production. Given the rise of machine monitoring solutions and industrial Is MES Holding You Back? Many companies have traditionally relied upon a Manufacturing Capacity Planning: Optimizing With such a wide variety of challenges impacting the current state of manufacturing, it can be difficult to plan for the future. American Manufacturing. The benefits in cost, efficiency, and improved profit margins make IIoT a necessity for doing business in manufacturing.

But as technology has advanced, many manufacturers continue to operate as they have in the past. Many methodologies, such as Lean and Six Sigma, are designed to help eliminate waste and improve processes in an operation. Operational Excellence to continuously improve our work processes, Reducing our scrap rate is one of our key areas in achieving. Keeping this cookie enabled helps us to improve our website. Its industrial material handling containers serve many industries including aerospace, defense, medical and automotive. Understand if production runs will stay within scrap targets and receive actionable alerts if scrap rates are trending too high. Your documentation will be digital and instantly accessible in its most current and accurate form to prevent the use of outdated information. This includes CAD and CAM drawings and any other engineering specifications. Scrap is aligned with process data because these areas are typically measured differently and at different granularities. However, to further improve our production process with a focus on reducing the scrap rate, we established several strategic and systematic enhancement processes. Machine learning algorithms leverage factory data from CAD drawings, machines and sensors along with quality systems to create a digital thread of your manufacturing processes. You hand the task of creating the part to two teams of workers, team A and team B. This means that every time you visit this website you will need to enable or disable cookies again.

We also analyzed all units related to the production process from management, product appliance, and equipment issues to material and environmental issues and communicated production and engineering changes throughout our supply chain and to our customers. Consult with a mechanical engineer from Marlin Steel today to learn how you can further improve your production process to make it ultra-efficient and reduce scrap production. These huge volumes of disparate data types and sources have encouraged manufacturers to implement platforms to collect and standardize data across their many machines and systems. Manufacturing scrap is the unusable material from a manufacturing operation that will be discarded. Choose the right tool for the job to create precise components with minimal waste.

The quality of a manufacturer depends not only on the quality of material and components used to make goods but also on the quality of material used in production tools. Operators, technicians, and managers relied upon a sea of charts, graphs, forms, and hand-written notes to understand where production processes were at for the shift, day, or week. Processes, data and bill of materials (BOM) change over time so predictive models must be updated to adapt to these changes. If youre using a low-quality sheet of alloy, then its likely that some pieces will be rejected due to material quality. Find materials, components, equipment, MRO supplies and more. Stamping shops can use offal dies (otherwise known as recovery dies) that use scrap to produce other parts, stitching or fastening scrap together to create a continuous strip. Inefficient container designs contribute to part damage and scrap production during late-stage production processes such asultrasonic parts cleaningor heat treating. For example, adding a soft polymer coating to an ultrasonic cleaning basket can prevent metal-to-metal contact during the cavitation processeliminating the risk of scratches and dents that cause parts to be scrapped or need remanufacturing. Of all the components comprising the cost structure of manufactured goods, material cost is one of the most expensive for almost any industry. We will continue to measure our business operations impact on the environment and set targets for continuous improvement. Scrap prediction models are run against live production data to project scrap rates if operators continue with current process settings and output. High scrap rate can be related to several issues. With MachineMetrics, workflows can be built and added to the system using a Triggers and Actions function to customize and automate many factory operations.

But when it comes to the most critical aspects of documentation, theyre lacking. California Do Not Track Notice. Production Visibility: How to Unlock Real-Time Shop Floor Unlocking Accurate Standardized Work with Production Data, capturing accurate production data at the machine level, 8 Wastes of Lean Manufacturing | MachineMetrics, 5 Lean Techniques That Will Improve Your Manufacturing Processes, Takt Time vs Cycle Time vs Lead Time | Definitions and Calculations, Emerging Industry 4.0 Technologies With Real-World Examples. Say that you have a part that you need to produce, and want to optimize the process to eliminate scrap and save money. Other tools that you might want to take a closer look at include the containers that you use to hold your parts through the production process. Using MachineMetrics to lower scrap is part of the platform's wide range of benefits. Advanced machine monitoring technology and analytics software from MachineMetrics can help companies move from preventive to predictive maintenance strategies to identify potential scrap and act before it happens. (In theory, this is the opposite of first-pass yield, which looks at the number of usable, or quality units produced divided by the total number of units produced). Scrap reduction techniques include auditing processes, root cause analysis, and other formal procedures to drive change. This can help quality managers and continuous improvement leaders adjust processes to ensure the most common causes of scrap are mitigated. With MachineMetrics, manual document movement can be a thing of the past. This helps drill down to the root cause faster to prevent scrap in the future. Theyll make smarter use of your resources, and not have to go through nearly as many trial and error experiences to find out what does and does not work.

With tool monitoring, settings can be monitored at a level beyond human detection. Good communication and collaboration between engineers, production team members, and materials suppliers are key, along with the use of simulation software to minimize the number of prototypes required. Documentation is a key part of change management, particularly in terms of information sharing and version control. Thomas Regional are part of Thomasnet.com. In our. As sensor technology evolved, the devices were improved to collect data from individual machines so companies could use the data to analyze production processes and identify areas for improvement. Manufacturing scrap is often considered an inevitability, something that just happens as a natural consequence of the manufacturing process. The problem with these minimalist container designs is that they fail to take into account the specifics of the manufacturing process and the design of the parts they hold. Theyre further aided by work instructions that help them conduct and understand the process undertaken. Many manufactured goods are produced in stages of a production process, and the failure at any one step can mean that the part must be rejected. For example, here at Marlin Steel, we use a number of different machines to cut and shape steel sheet metal, including: The choice of machine to use depends on a number of factors, such as whether or not the sheet metal needs to be bent into specific shapes. Third-party contract manufacturers should be provided with a complete suite of documentation including BOM records, CAD sheets, details of changes, datasheets, and work instructions.

Planning Master suggests incorporating estimates of these wastes to generate a more accurate scrap rate: Scrap can be caused by a range of factors and is often a result of poor processes. In the case of the former, a rigorous selection of materials such as tensile strength, alloy consistency, and vendor's production methods can make or break a company's quality when those materials are in production. Company. Engineers or shift supervisors can quickly identify the root cause of high projections and make adjustments in real time to eliminate scrap before rates increase to unprofitable levels. We also have internal processes to recycle supporting production materials such as oil and water.

Or just share your thoughts on my blog post, which I hope was somewhat helpful in how to understand and reduce scrap rate. Because a small amount of scrap is inevitable, its important to find out whether you can reuse or recycle your raw material. Your email address will not be published. To ensure our business performance was kept at a long-term, solid, and healthy level, the management team set up a clear target for improvements. Scrap is often the outcome of poor or incomplete communication about production changes. Combined with high-frequency data analysis, staff can see undetected problems before they occur. The issue is so critical that, similar to labor and equipment utilization, programs to reduce scrap are almost always part of manufacturers continuous improvement initiatives.
Sitemap 2